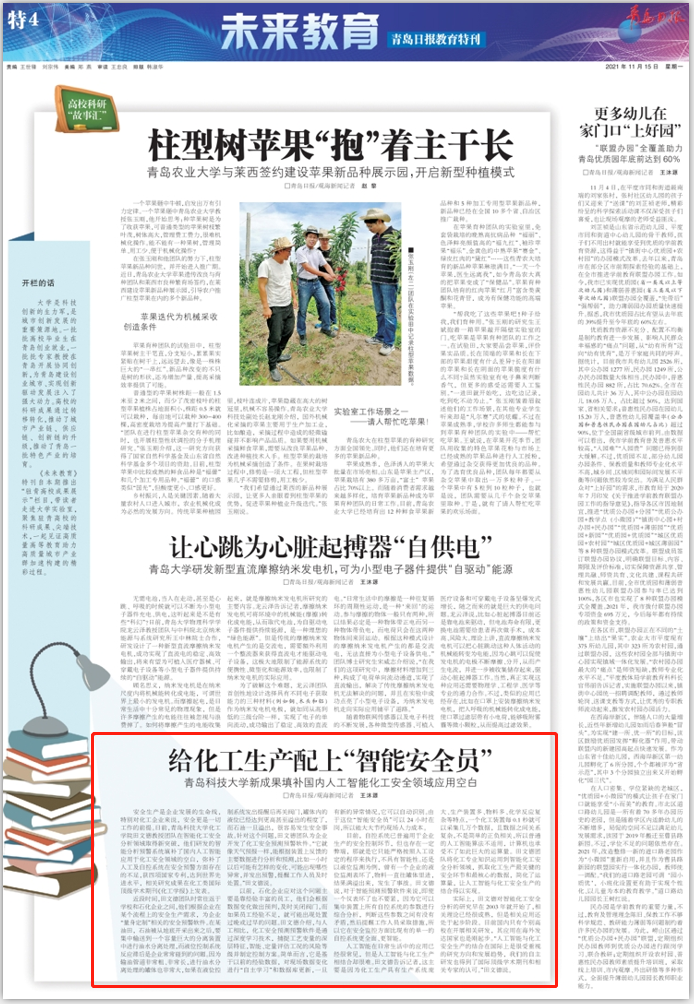
安全生产是企业发展的生命线,特别对化工企业来说,安全更是一切工作的前提。日前,青岛科技大学化工学院田文德教授团队在智能化工安全分析领域取得新突破,他们研发的智能分析预警系统填补了国内人工智能应用于化工安全领域的空白,弥补了人工及自控系统在安全预警方面存在的不足,获四项国家专利,达到世界先进水平,相关研究成果在化工类国际顶级学术期刊《化工学报》上发表。
近段时间,田文德团队时常往返于学校和石化企业之间,他们根据企业在某个流程上的安全生产需求,为企业“量身定制”相关的安全预警软件。在某油田,石油被从地底开采出来之后,要集中输送到一个容量巨大的分离装置中进行油水分离处理,而液位控制系统反应滞后是企业常常碰到的问题。因为输油管道非常粗、非常长,进行油水分离处理的罐体也非常大,如果在液位控制系统发出提醒后再关阀门,罐体内的液位已经达到更高甚至溢出的程度了,而石油一旦溢出,很容易发生安全事故。针对这个问题,田文德团队为企业开发了化工安全预测预警软件。“它就像天气预报一样,能根据装置上反馈的主要数据进行分析和预测,比如一小时以后可能有怎样的变化、可能出现哪些异常,并发出预警,提醒工作人员及时处置。”田文德说。
以前,石化企业应对这个问题主要是靠经验丰富的员工,他们会根据数据变化做出预判,及时关闭阀门,而如果员工经验不足,就可能出现处置过晚或过早的问题。田文德介绍,与人工相比,化工安全预测预警软件是通过深度学习技术,捕捉工艺变量的深层特征,智能、定量评估工况的风险等级并制定控制方案。简单而言,它是基于以前的经验数据,对现场数据变化进行“自主学习”和数据库更新,一旦有新的异常情况,它可以自动识别。由于这位“智能安全员”可以24小时在岗,所以能大大节约现场人力成本。
目前,自控系统已普遍用于企业生产的安全控制环节,但也存在一定弊端,那就是它只能严格按照人工设定的程序来执行,不具有智能性。还是以液位监测为例,曾有一个企业的液位监测表坏了,物料一直往罐体里进,结果满溢出来,发生了事故。田文德说,对于智能预测预警软件来说,即使一个仪表坏了也不要紧,因为它可以集中装置上所有自控系统的参数进行综合分析,判断这些参数之间有没有矛盾,然后提醒工作人员采取措施,所以它在安全监控方面比现有的单一的自控系统更全面、更智能。
人工智能在日常生活中的应用已经很常见,但是人工智能与化工生产相结合却很难。田文德告诉记者,这主要是因为化工生产具有生产系统庞大、生产装置多、物料多、化学反应复杂等特点,一个化工装置每0.1秒就可以采集几万个数据,且数据之间关系复杂,不是简单的正负相关,所以普通的人工智能算法不适用,计算机也承受不了如此巨大的运算量。田文德团队将化工专业知识运用到智能化工安全分析领域,抓取化工生产最关键的安全环节和最核心的数据,简化了运算量,让人工智能与化工安全生产的结合得以实现。
实际上,田文德对智能化工安全分析的研究早在2003年就开始了,相关理论已经很成熟,但是相关应用还处于起步阶段。目前国内只有个别高校在开展相关研发,其应用在海外发达国家也是刚起步。“人工智能与化工安全生产的结合在国际上是很受重视的研究方向和发展趋势,我们的自主研发也得到了国际顶级学术期刊和相关专家的认可。”田文德说。